Wastewater Treatment System for Chemical Etching Plants
Chemcut manufactures a batch wastewater treatment system to support Chemcut wet process systems. Our wastewater treatment process utilizes ion exchange and/or sequential batch technologies that follow specific wastewater treatment steps.
Chemcut’s wastewater treatment systems are made of corrosion-resistant materials suitable for use in etching plants and other corrosive locations. They are designed for manual control for facility-wide or point-of-source applications.
Wastewater Treatment System Options
- Batch Wastewater Treatment
- Cascade Rinse
- Closed-Loop Systems
- Cooling Water Reduction
- Electrowinning system is available in conjunction with ion-exchange
- Filtration
- Ion-Exchange Systems
- Point of Source Treatment
- Rinse Water Conservation
- Filter Press
Ion Exchange System
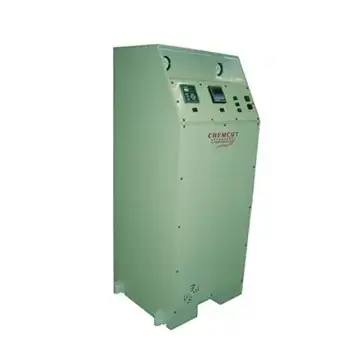
- Closed-loop system
- Decrease your water usage by connecting an ion exchange to your rinse water
Why Should You Use Chemcut’s Wastewater Treatment System?
Our wastewater treatment systems have been recognized twice by the Pennsylvania Governors Award for Environmental Excellence.
Our systems are designed for reducing operating costs, minimizing maintenance costs, and saving water. We will provide you with the proper steps to treat your wastewater with our system.
Rinsewater Conservation
Cascade Rinse
We have designed an efficient cascade rinse that can be used after every chemical station to reduce the chemistry load on the wastewater treatment unit.
The most important chemistry to reduce is stripping chemistry, which can generate complex metal ions and make them difficult to remove from the water.
Ion Exchange
For customers interested in lowering their water usage, we have a closed-loop cascade rinse system. The cascade system is paired with an ion-exchange unit that allows you to run an etcher rinse without adding water. The only water that will need to be added to a closed-loop system is water that is lost to evaporation.
Depending on the rate of metal loading, ion exchange resin (columns) will need to be regenerated on occasion. In conjunction with an electrowinning cell, copper can be recovered during the regeneration process by plating the copper out in an acidic state. (Not used for ferric chloride etching)
Batch Wastewater Treatment
Even if you have a closed-loop system on the etcher, you will need to treat the waste from spills and other wet processing equipment. We are here to make sure your etching plant is a success and will provide you with the steps to wastewater treatment that our experts have developed.
The wastewater treatment system we offer collects the liquid that exits the wet processing equipment and transfers it to a “wastewater collection tank.” When there is enough wastewater to run a batch treatment, the waste can be transferred into the “reaction tank.”
In the reaction tank, the pH will be adjusted and a flocculent and polymer will be added to the water. These chemicals will react causing the heavy metals to coagulate and settle at the bottom of the tank. The clear water can then be decanted, and the sludge (coagulated heavy metals and polymer) will be discharged through the Filter Press.
This system is capable of processing waste rinse water from ferric chloride etching, cupric chloride etching, and various other metal etching rinses. It is not designed to handle concentrated wastes, however.
Please contact us to request a detailed breakdown of our “steps to wastewater treatment process.”
Cooling Water Reduction
Chemcut sumps are designed for optimal stirring of etchant or other chemistries. The stirring helps to lower the required amount of cooling water and will reduce the electricity used to heat the etching chemistry.
The addition of a re-circulation pump will increase the stirring of the chemistry in the sump, increasing the cooling efficiency.
MADE IN THE USA
Related Resources
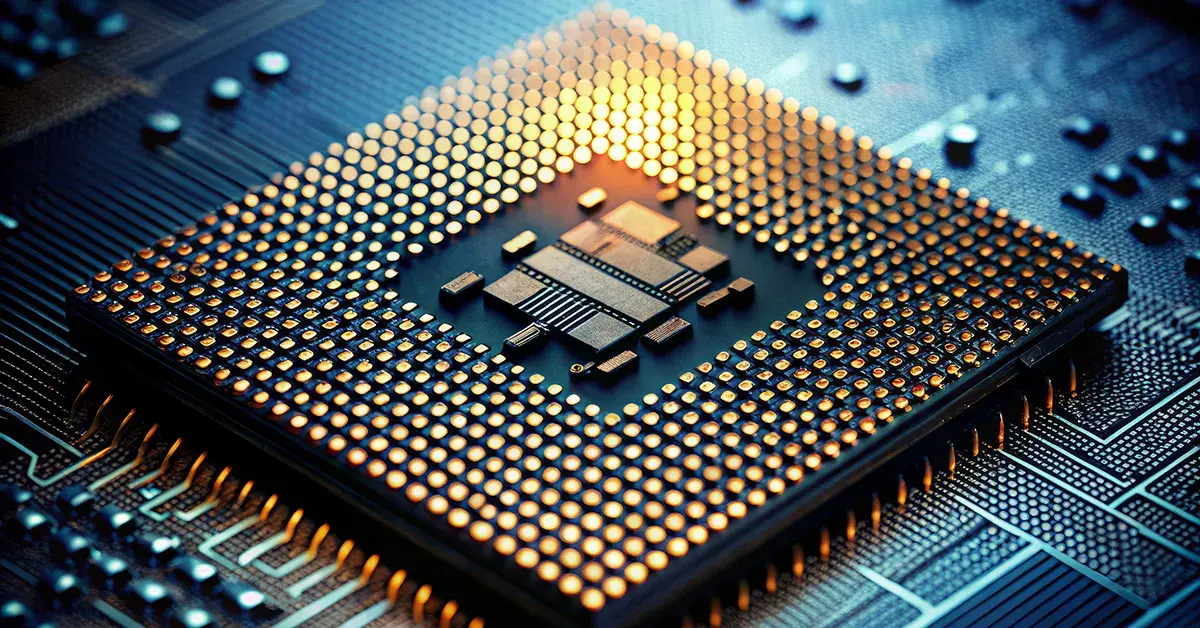
How to Scale Up Production with Chemical Milling & Etching
Chemical milling and etching are powerful techniques widely used in industries requiring precise,...
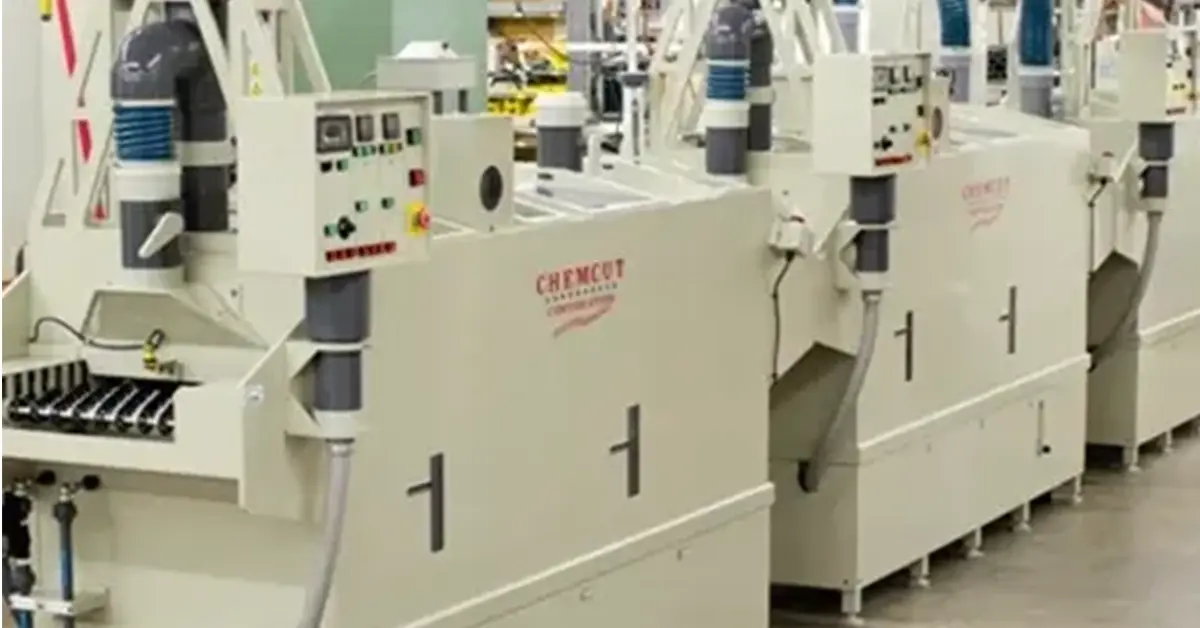
11 Things Needed to Start a Chemical Etching Plant | Chemcut Blog
11 Things You Need to Start a Chemical Etching Plant Chemical etching has been around since 2500...
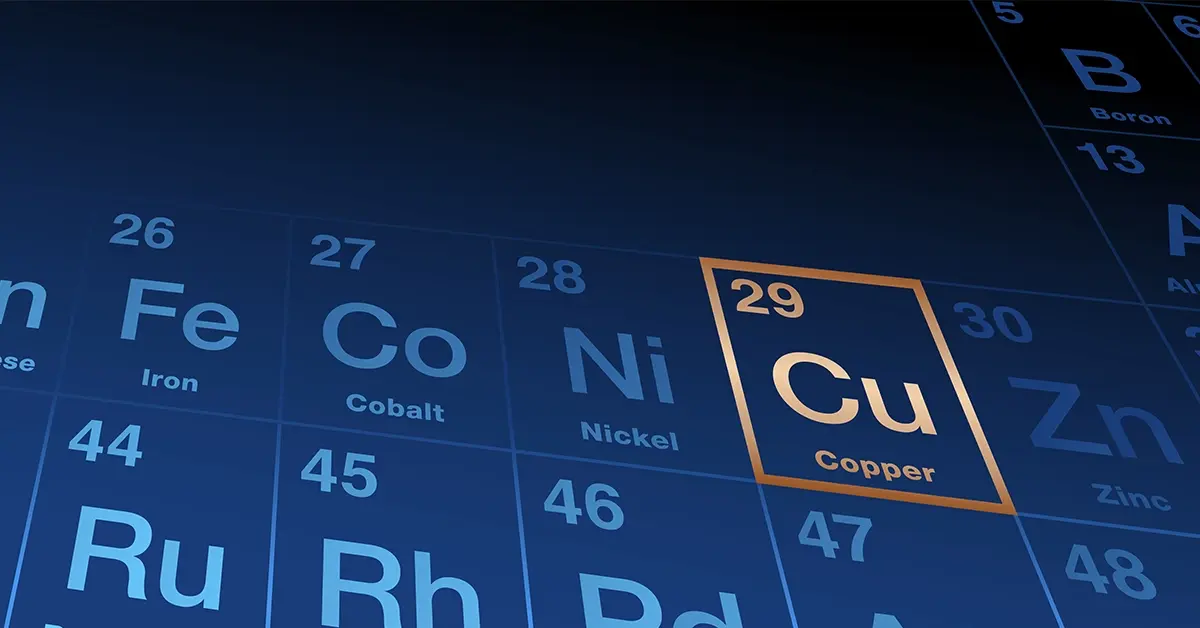
Copper Etchant Options | ChemCut
Copper etching is a vital manufacturing process that tends to be used in the manufacturing of...
High quality products are made with high quality equipment. Stake your reputation on Chemcut.
Already a customer?
Chemcut’s commitment to you goes beyond the sale. We keep your equipment running with the industry’s best post-sales support, which includes our in-house R&D lab and global field service assistance.
We also maintain the industry’s largest and most diverse inventory of high-quality replacement parts to ensure prompt delivery regardless of the type or age of your Chemcut or MEI Division equipment.