Regeneration for Copper Chloride and Ferric Chloride Etching
Product Lines for Etchant Regeneration
Our Etchant Regeneration equipment can be customized to accommodate your unique process easily. Review the options, then speak with one of our experts about developing the custom solution you need.
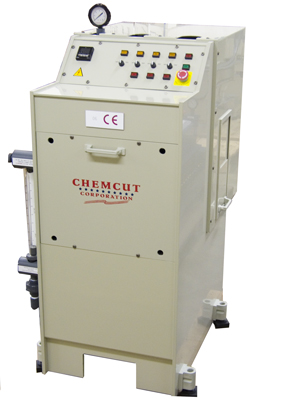
XLi Etching Systems
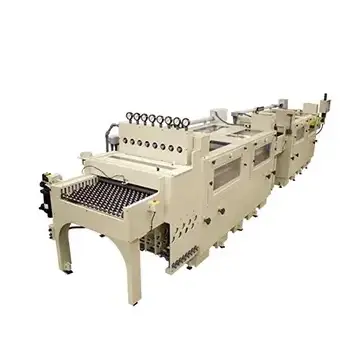
- 20″
- 30″
- 40″
- 50″
- 60″
- Custom Size (1 to as many chambers as you want)
- DES (Develop – Etch – Strip)
- Etcher (Stand Alone)
- SES (Strip – Etch – Strip)
- Alkaline Etchant
- Cupric Chloride Etchant
- Ferric chloride Etchant
- Hydrofluoric Acid (HF)
- Micro etch
- Aluminum
- Copper
- Glass
- Steel
- Titanium
- And more
2300 Series Etching System
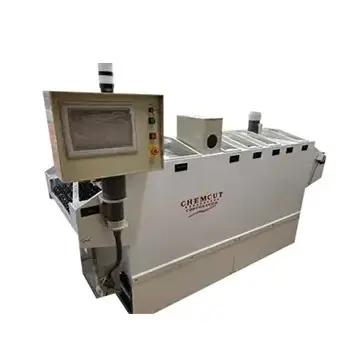
- 15″
- 20″
- 30″
- Custom Size (1 to as many chambers as you want)
- DES (Develop – Etch – Strip)
- Etcher (Stand Alone)
- SES (Strip – Etch – Strip)
- Alkaline Etchant
- Cupric Chloride Etchant
- Ferric chloride Etchant
- Hydrofluoric Acid (HF)
- Micro etch
- Aluminum
- Copper
- Glass
- Steel
- Titanium
- And more
CC8000 Etching Systems
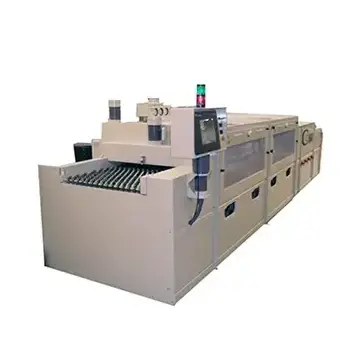
- 20″
- 30″
- 40″
- 50″
- 60″
- Custom Size (1 to as many chambers as you want)
- DES (Develop – Etch – Strip)
- Etcher (Stand Alone)
- SES (Strip – Etch – Strip)
- Alkaline Etchant
- Cupric Chloride Etchant
- Ferric chloride Etchant
- Hydrofluoric Acid (HF)
- Micro etch
- Aluminum
- Copper
- Glass
- Steel
- Titanium
- And more
Etchant Regeneration Systems from Chemcut
Chlorine Gas
Sodium Chlorate and Hydrochloric Acid
Hydrogen Peroxide and Hydrochloric Acid (Cupric Chloride only)
Chemcut patented the etchant regeneration process more than 50 years ago (Patent #3,526,560), and, since that time, we have delivered approximately 1,000 copper chloride (cupric chloride) and ferric chloride regeneration systems worldwide.
Adding a regeneration system to your metal etching system will extend the life of a ferric chloride metal etcher by threefold.
Adding a regeneration system to your cupric chloride metal etcher will extend the etchant’s life indefinitely, as long as the dosing is correct, and we will help you set up the dosing correctly.
Chemistry Regeneration Capacity
Our equipment can regenerate up to 1,000 pounds of metal per day. Need more? We can build a system to meet your regeneration need.
All Chemcut acid regeneration systems for copper and ferric chloride use oxidation-reduction potential (ORP) and specific gravity control.
Automatic control of hydrochloric acid content is optional.
System Controls for Chemistries that Cannot be Regenerated
In addition to acid regeneration systems for copper and ferric chloride acid, Chemcut also offers system-integrated chemistry control routines for ammonia-based etchants, micro-etch applications, developer, stripping, chemical cleaning, and many other solutions.
The following automatic chemistry control systems are the most common, but not the only systems we can build:
- Bath Control (feed and bleed system)
- pH Control
- Panel Count
How Does the Regeneration of Etchant Work?
Etching metal causes the in-solution metal content to increase. To continue etching metal, the chemicals that are being depleted by etching need to be replaced.
The ORP and Free Acid are very important to maintaining a working etching bath and stopping the chemistry from crystalizing. Unfortunately, etching metal with cupric chloride and ferric chloride causes the ORP and Free Acid to decrease.
To cause a regeneration reaction, a specific mixture of chemicals is added to the spent/used etchant to make the etchant active again. For cupric and ferric chloride, the specific mixtures create chlorine gas, and it reacts with the used etchant to restore it back to its active phase.
This extends the life of etchant significantly and is an easy process to implement when using a Chemcut system. The specific mixtures used to regenerate cupric and ferric are explained below.
Chlorine Gas
Regeneration using chlorine gas is the simplest system when it comes to chemistry. Chlorine gas is pumped into the cupric chloride or ferric chloride. The chlorine gas reacts with the spent etchant to regenerate the free acid and cupric or ferric chloride.
Chlorine gas systems also need a water input to keep the specific gravity under control. Then the etchant is once again ready to etch metal.
Sodium Chlorate
Using our sodium chlorate system is more complicated when it comes to chemistry but is not difficult if you are using a Chemcut system. Sodium chlorate, hydrochloric acid, and water are all pumped into the bath.
The sodium chlorate and hydrochloric acid react to create chlorine gas. The chlorine gas then reacts with the used acid to regenerate the free acid and etchant to make the etchant active again and ready for metal etching.
Hydrogen Peroxide (Copper Chloride Etching Only)
This regeneration system only works for copper chloride and, like sodium chlorate, has two different chemistries.
Hydrogen peroxide and hydrochloric acid will be the two chemistries pumped into the bath. The hydrogen peroxide and hydrochloric acid will react to create chlorine gas and water. The chlorine, like the two reactions above, will make the used etchant active again and the water will keep the specific gravity down. Making the acid ready to etch metal again.
If you would like more information on the copper chloride formula and ferric chloride formula, please contact us. We can explain the exact reaction that takes place to regenerate the copper etchant to the original copper chloride formula. The same applies to the ferric reaction when etching stainless steel and other metals.
Chemistry Parameter Recommendations When Using Regeneration
ORP: For cupric chloride and ferric chloride, we recommend keeping the ORP within 550–590. It is common for chemical millers to run ferric chloride at 600.
Free Acid: For cupric chloride etching, we recommend keeping the free acid level between 1–2N HCl.
Ferric chloride: Ferric chloride is extremely difficult to measure once the chemistry is used. We recommend doing a visual check through the sight glass. Ferric chloride will become turbid when the acid level is low. Fairly simple titration methods are available to determine free acid in ferric chloride.
If you are specifying a new etcher, a regeneration system for your new etcher can be built into the etchant chamber(s), rather than as a free-standing unit.
If you are adding regeneration to an existing etcher, knowing your expected metal loading is important so a properly sized system can be recommended.
Related Resources
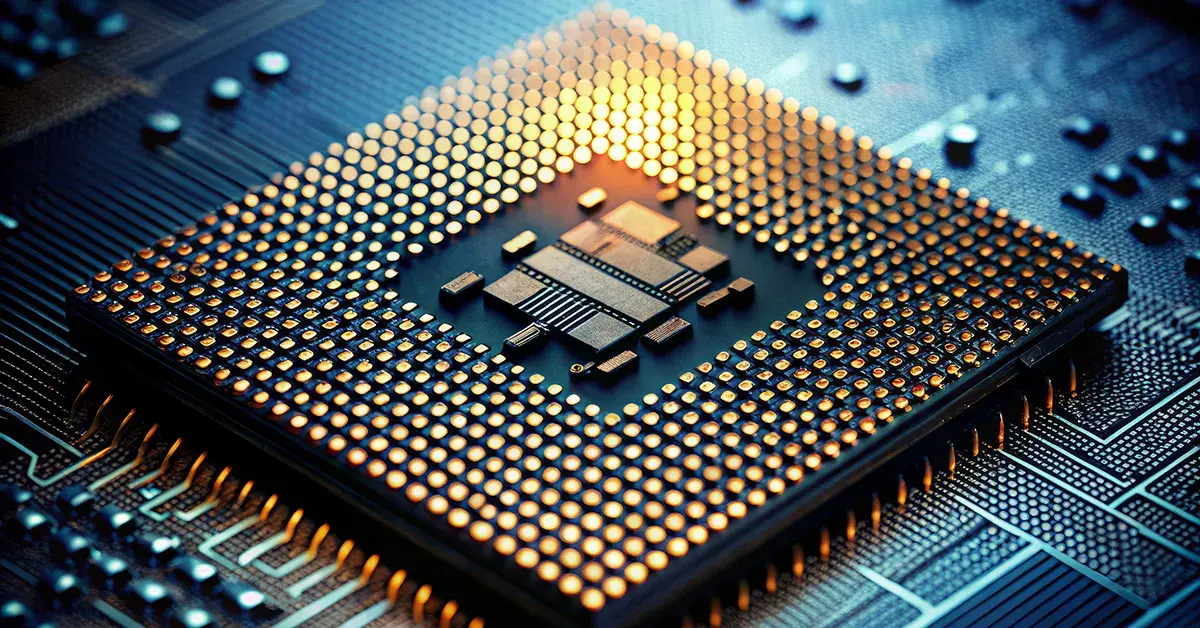
How to Scale Up Production with Chemical Milling & Etching
Chemical milling and etching are powerful techniques widely used in industries requiring precise,...
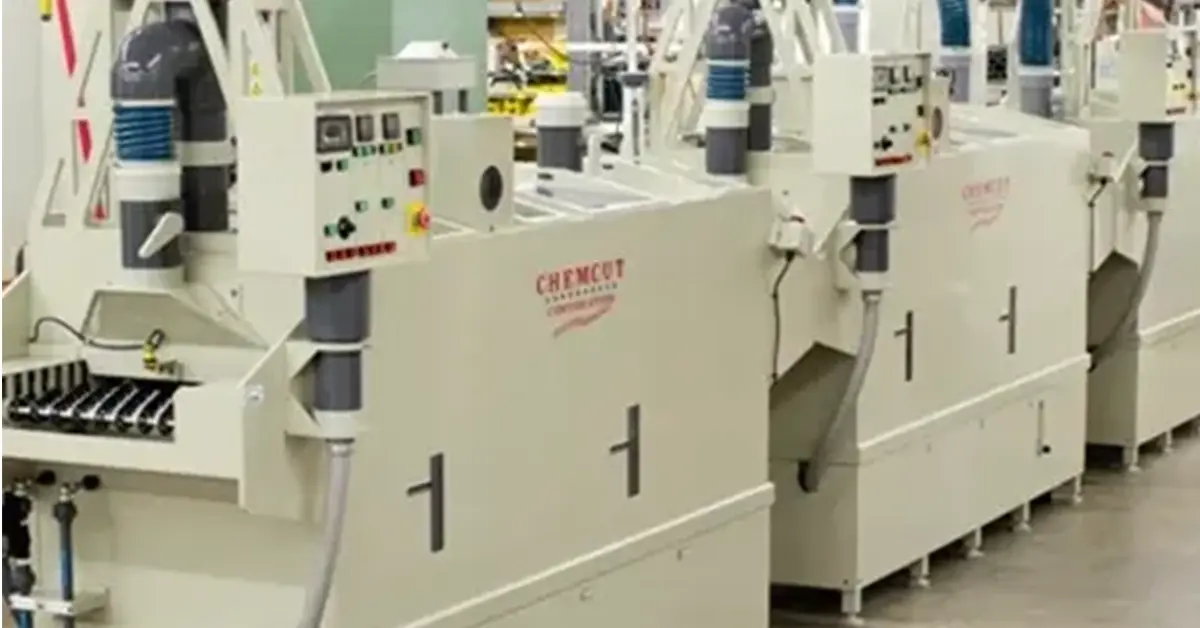
11 Things Needed to Start a Chemical Etching Plant | Chemcut Blog
11 Things You Need to Start a Chemical Etching Plant Chemical etching has been around since 2500...
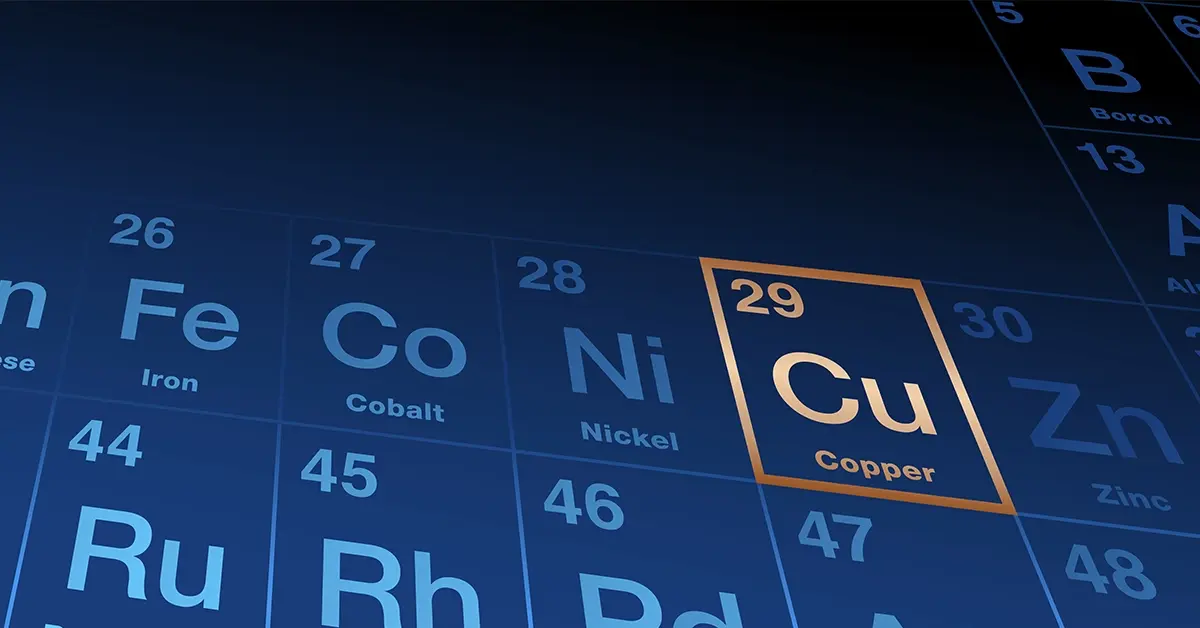
Copper Etchant Options | ChemCut
Copper etching is a vital manufacturing process that tends to be used in the manufacturing of...
High quality products are made with high quality equipment. Stake your reputation on Chemcut.
Already a customer?
Chemcut’s commitment to you goes beyond the sale. We keep your equipment running with the industry’s best post-sales support, which includes our in-house R&D lab and global field service assistance.
We also maintain the industry’s largest and most diverse inventory of high-quality replacement parts to ensure prompt delivery regardless of the type or age of your Chemcut or MEI Division equipment.