Chemical Cleaning & Brushing Machines
Chemical Metal Cleaning
Acid & Alkaline Cleaning Processes
Chemical cleaning for sheet metal etching has two different processes: alkaline clean and acid clean.
While not all sheet metals require both cleaning processes, in a process that requires both, alkaline clean is the first step, removing all oils and organics from the surface.
Acid cleaning is the second cleaning step. An acid clean is used to remove any contaminants that remain on the metal’s surface. Some metal surfaces will be micro-etched from this chemistry, which helps with photoresist adhesion.
The cleaning process is essential to attain your ceramic and metal etching goals. If the surface is not properly cleaned, the photoresist will not lock into the material, and when the material is being etched the photoresist will lift, causing your parts to fall outside your tolerances.
A second reason for cleaning the surface is to remove all dirt particles. If the particles are not removed, they can interfere with the exposure step, resulting in opens for PCBs or etched areas that were supposed to be unetched for chemical milling/glass etching.
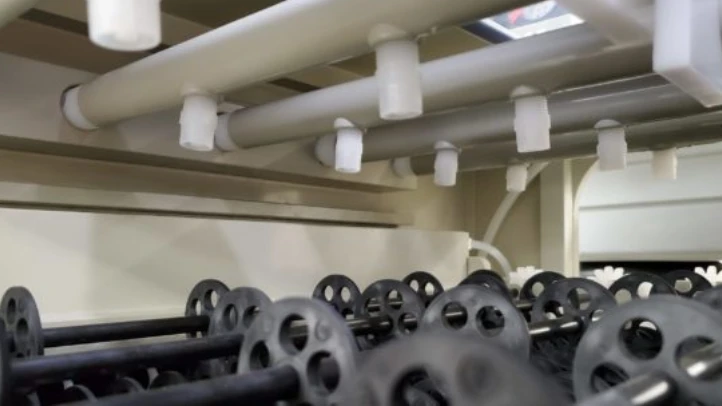
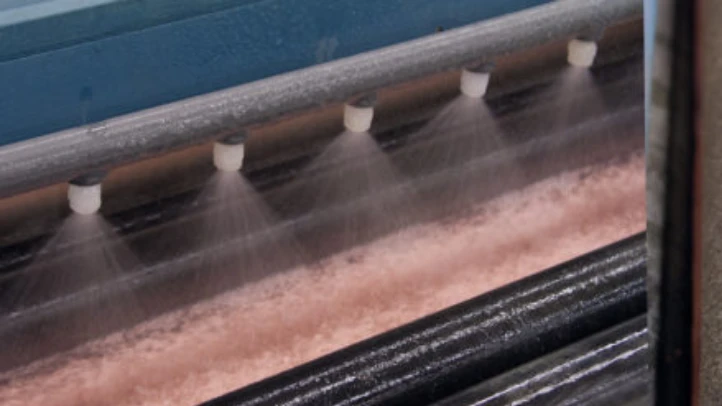
Electrolytic Cleaner for PCB
Electrolytic cleaning is a common cleaning process for the fabrication of PCB and is used to remove the chromate layer on PCB/copper foil.
Cleaning copper foil electrolytically before micro etching is important to make sure the chromate layer does not interfere with the micro etching process.
Ultrasonic Cleaner Machine
If your process requires a VERY clean product, we meet the need with our ultrasonic cleaner. The most common use of a Chemcut ultrasonic cleaner machine is for cleaning PCB.
Multi-layer PCB boards need to have perfectly cleaned holes to make sure there is no break in the copper connectors. Therefore, PCB fabrication shops use our ultrasonic PCB cleaning machine to clean the holes and ensure a quality connection.
XLi Chemical Cleaning System
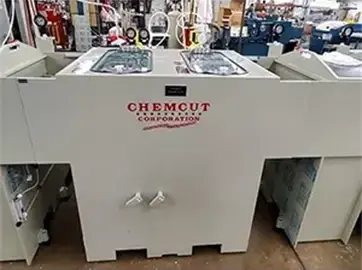
- 20″
- 30″
- 40″
- 50″
- 60″
- Cleaner (Stand Alone)
- Alkaline Clean to Acid Clean
- Custom Size (1 to as many chambers as you want)
- Acid Cleaner
- Alkaline Cleaner
121 Brush Cleaner
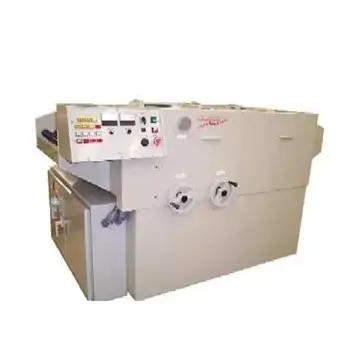
- Wet Brushing
- Oscillating Brushes
- Choice of bristle or compressed brushes
- Brushing
- Cleaner
- Finishing
- Remove Polishing
219 Scrubber
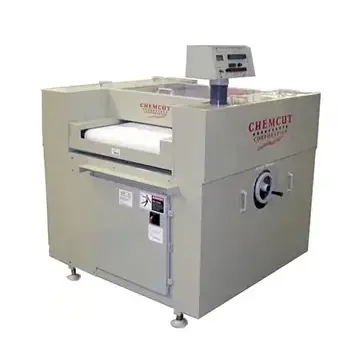
- Single-sided abrasive brush
- Tough reinforced conveyor belt supports small parts
2300 Series Chemical Cleaning System
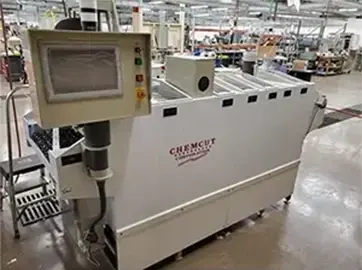
- 15″
- 20″
- 30″
- Cleaner (Stand Alone)
- Alkaline Clean to Acid Clean
- Custom Size (1 to as many chambers as you want)
- Acid Cleaner
- Alkaline Cleaner
604 Deburrer
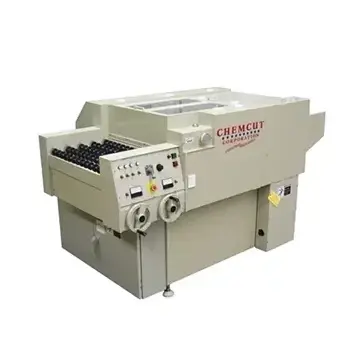
- 2 oscillating brushes
- Built-in Rinse and Dryer
- Post PCB drilling
- Post punching operations
CC8000 Chemical Cleaning System
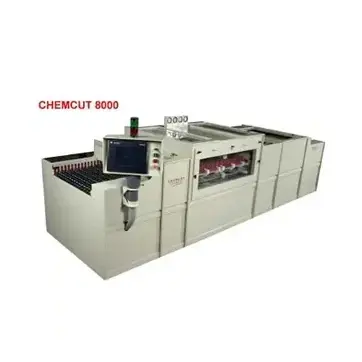
- 20″
- 30″
- 40″
- 50″
- 60″
- Cleaner (Stand Alone)
- Alkaline Clean to Acid Clean
- Custom Size (1 to as many chambers as you want)
- Acid Cleaner
- Alkaline Cleaner
Mechanical Metal Cleaning Machine Options
Our mechanical cleaners were first used to scrub PCB surfaces.
Less aggressive than the mechanical deburr, our Scrubber is used to clean the metal surface and creatie a uniform, parallel grained-finished surface.
The Mechanical Deburr is typically used on rigid metals and PCBs after drilling to deburr the holes. Deburr is more aggressive than the scrubber and will result in a uniform, parallel grain-finished surface like the scrubber.
The scrubber and deburr have both evolved into a mechanical glass cleaner, wafer cleaner, and metal cleaner for chemical milling.
Product Lines
Each piece of Chemcut equipment is customized, so your process will be unique to you.
Related Resources
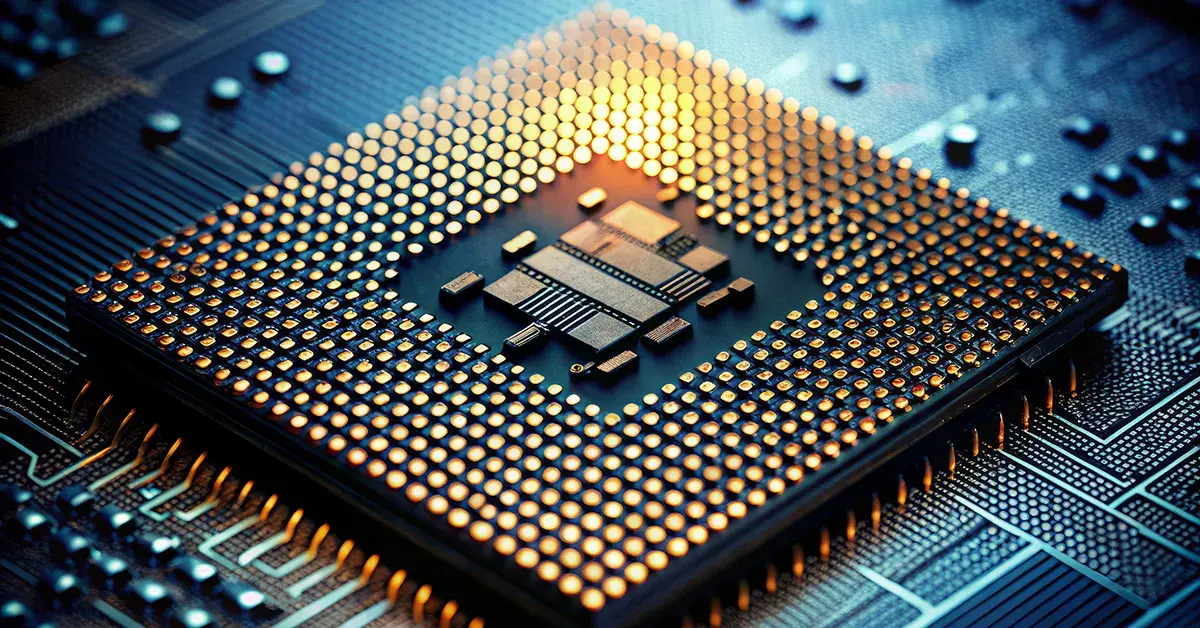
How to Scale Up Production with Chemical Milling & Etching
Chemical milling and etching are powerful techniques widely used in industries requiring precise,...
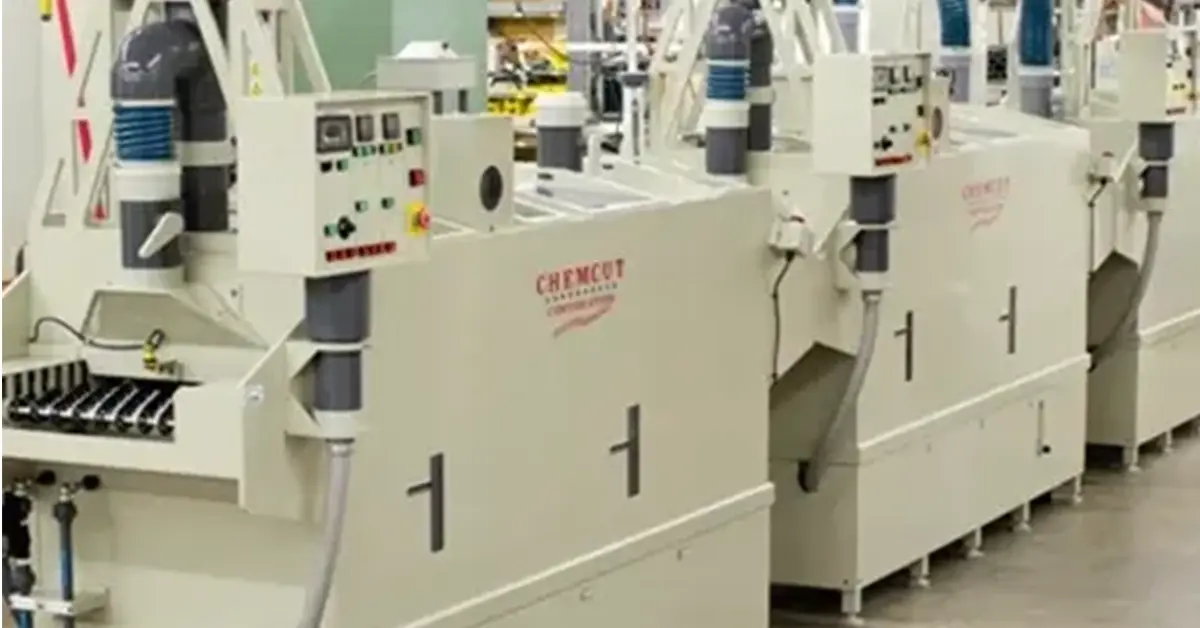
11 Things Needed to Start a Chemical Etching Plant | Chemcut Blog
11 Things You Need to Start a Chemical Etching Plant Chemical etching has been around since 2500...
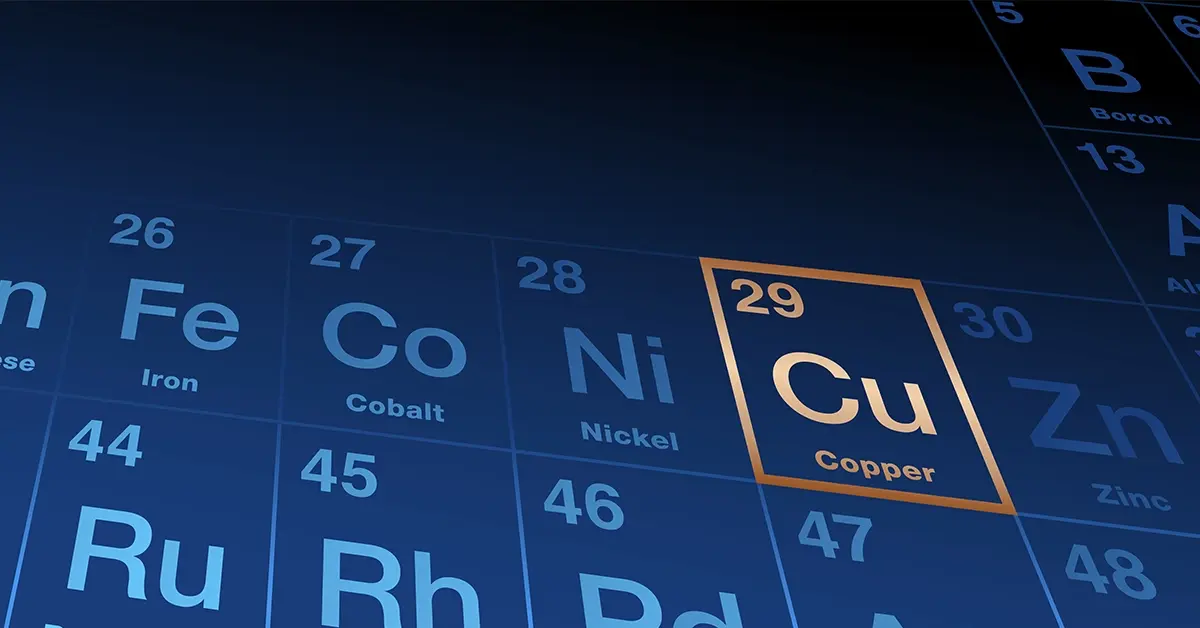
Copper Etchant Options | ChemCut
Copper etching is a vital manufacturing process that tends to be used in the manufacturing of...
High quality products are made with high quality equipment. Stake your reputation on Chemcut.
Already a customer?
Chemcut’s commitment to you goes beyond the sale. We keep your equipment running with the industry’s best post-sales support, which includes our in-house R&D lab and global field service assistance.
We also maintain the industry’s largest and most diverse inventory of high-quality replacement parts to ensure prompt delivery regardless of the type or age of your Chemcut or MEI Division equipment.