How to Scale Up Production with Chemical Milling & Etching
Chemical milling and etching are powerful techniques widely used in industries requiring precise, high-quality production processes. These methods involve controlled removal of material to create intricate designs and features, making them ideal for manufacturing components with tight tolerances.
For engineers like you, moving from a prototype to full-scale production is a critical phase. This transition not only demands maintaining the integrity and quality of your product but also optimizing the process to enhance productivity, yield, and throughput while managing costs. Understanding how to effectively scale up using chemical milling and etching is essential to achieving these goals.
Understanding the Prototype Phase
The prototype phase is a critical step in the development of any new product. It's where ideas are transformed into tangible models, allowing engineers to validate the design, functionality, and feasibility of their concepts. Prototypes serve as the blueprint for full-scale production, ensuring that every detail has been accounted for before committing to mass manufacturing.
However, rushing through this phase without thorough validation can lead to significant issues down the line. Inadequate testing and refinement of a prototype can result in design flaws or inefficiencies being magnified during production, leading to costly rework, delays, or even product failure.
By taking the time to rigorously test and validate your prototype, you can identify and address potential pitfalls early on, paving the way for a smoother transition to large-volume manufacturing.
Key Considerations for Scaling Up Production
Scaling up production from a prototype to large-volume manufacturing requires careful planning and consideration of several key factors to ensure efficiency and success. As you move forward, here are some critical elements to keep in mind:
- Production Volume and Timing
Determining the required production volume and the time it will take to produce each part is crucial. Understanding how long each part needs to be etched and how many parts are needed will inform the design of the system and the overall production schedule. Efficiently matching production capacity with demand ensures that the process scales effectively without bottlenecks. - In-House Production vs. Outsourcing
Deciding whether to manufacture in-house or outsource is another significant consideration. If you choose in-house production, you’ll need to invest in the appropriate equipment and technology for chemical milling and etching. On the other hand, outsourcing may simplify operations but could reduce your control over quality and lead times. Weigh the pros and cons of each option based on your specific needs and capabilities. - Material and Design Specifications
The thickness and material composition of the parts play a pivotal role in the etching process. For instance, if the material is too thick, it might not be suitable for chemical etching. Additionally, if the prototype was created using a different method, you’ll need to develop a photo tool to guide the etching process. Ensuring that the design and material are compatible with etching will prevent issues during production. - Optimization of Sheet Layout
When scaling up, it’s essential to optimize the layout of your parts on the metal sheets. Larger sheets allow for more parts to be processed simultaneously, improving efficiency. However, they can also present challenges in aligning and transferring specifications accurately. Balancing sheet size with ease of handling and precision is key to maximizing production efficiency. - Feasibility Studies
Before fully committing to scaling up, conducting a feasibility study is a prudent step. This study will assess whether the etching process is the best method for your production needs and help identify any limitations. It’s also a good opportunity to explore alternative methods, such as stamping, and weigh their costs and benefits against etching. Feasibility studies ensure that the chosen process aligns with your production goals and can be scaled effectively.
Scaling Up Production with Chemical Milling & Etching
Optimizing Productivity and Throughput
When scaling up production using chemical milling and etching, optimizing productivity and throughput is essential to meet high-volume demands efficiently. Here are several strategies engineers can implement:
- Extend Dwell Time
One way to increase throughput is by extending the dwell time of parts within the machine. The etching process requires a specific amount of time for parts to be properly processed. By lengthening the machine’s path, you allow parts to stay in the etching environment longer. This allows you to increase the speed of the overall process without compromising quality, effectively boosting productivity. - Automate Chemistry Control
Manual control of the chemical process introduces the potential for human error, which can affect the consistency and quality of the output. Implementing automatic chemistry control systems helps maintain optimal chemical balance throughout the etching process, ensuring that every part meets specifications. This not only improves consistency but also enhances throughput by reducing downtime due to errors. - Adjust Machine Settings and Add-Ons
Fine-tuning machine settings and adding enhancements can significantly impact throughput and operational consistency. Engineers should explore available options for machine upgrades or add-ons that streamline the process. This could include features that allow for better handling of materials or improved coordination between different stages of the production line. - Optimize Waste Treatment
Managing waste efficiently is another critical factor in optimizing throughput. For example, controlling water usage during the etching process can reduce the load on waste treatment systems, minimizing bottlenecks. Understanding and optimizing the waste management aspects of your process can lead to more sustainable and faster production cycles.
Maximizing Yields and Quality
Maximizing yields and ensuring high-quality output are critical goals when scaling up chemical milling and etching processes. Here are some strategies to help you achieve these objectives:
- Leverage Automation Wisely
Automation is a powerful tool for enhancing both yields and quality, but it requires careful consideration. While automation can reduce human error and increase consistency, it comes with a higher cost. It’s important to strike a balance between the level of automation you need and what you can afford. Investing in the right amount of automation will help maintain high standards without overspending. - Assess Raw Material Quality
The quality of your raw materials has a direct impact on the final product. If you encounter quality issues during production, the problem might lie with the materials rather than the process. Ensure that your materials are rigorously tested before use, and consider switching suppliers if you experience consistent quality issues. High-quality raw materials are essential for achieving maximum yields and minimizing defects. - Understand the Role of Chemistry
The chemistry involved in the etching process plays a significant role in yield and quality. Variations in chemical composition, concentration, or temperature can lead to inconsistencies and lower yields. Regularly monitor and adjust the chemical parameters to ensure they are optimized for your specific application. Understanding the interplay between chemistry and the etching process will help you troubleshoot issues and maintain high-quality standards.
Cost Reduction Strategies
When scaling up production, managing costs without sacrificing quality or efficiency is crucial. Here are some strategies to help reduce expenses during the chemical milling and etching process:
- Water Conservation
One often overlooked area for cost reduction is water usage. Implementing water conservation techniques, such as recycling water after etching by removing contaminants like copper, can significantly reduce water consumption and associated costs. - Optimized Cooling Systems
Cooling costs can be a major expense in production. By installing temperature gauges on the input and output, you can monitor and adjust the cooling flow to operate more efficiently, potentially cutting cooling costs by 50% to 75%. Slowing down the flow while maintaining the necessary cooling effect is a simple yet effective way to save money. - Extend Chemistry Life Through Automation
Automation can also play a role in reducing costs by extending the life of the chemicals used in the etching process. Automated systems ensure that chemicals are replenished and maintained at optimal levels, reducing waste and the need for frequent chemical replacements. - Monitor Energy Usage
Regularly reviewing and optimizing energy consumption across your production line can reveal areas where costs can be cut. Simple adjustments, such as optimizing machine operation schedules or upgrading to more energy-efficient equipment, can lead to substantial savings.
Chemical Milling vs. Etching: Understanding the Difference
Chemical milling and etching are both precision manufacturing processes used to create intricate metal components by selectively removing material, but they differ in techniques, applications, and material compatibility, making it crucial to understand their distinctions for optimal production outcomes.
This section delves into the definitions, benefits, and key differences of each process to help you choose the best method for your specific needs.
What Is Chemical Milling?
Chemical milling, also known as chem milling or chemical machining, is a subtractive manufacturing process that removes layers of material from a workpiece using chemical etchants. This technique is typically employed to reduce the thickness of metal parts, create complex shapes, or achieve weight reduction without compromising structural integrity.
Applications of chemical milling are widespread, particularly in aerospace, automotive, and electronics industries, where precision and material integrity are crucial. The benefits include the ability to produce intricate designs, minimize mechanical stress on the material, and process large or thin parts that would be challenging to machine using traditional methods.
What Is Chemical Etching? 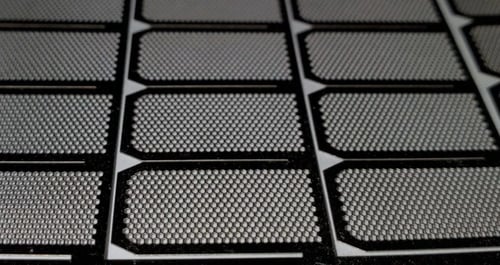
Chemical etching, also known as photochemical machining (PCM), is a process that uses chemical solutions to selectively remove material from the surface of a workpiece. Unlike chemical milling, which focuses on large-scale material removal, chemical etching is used for creating fine details and intricate patterns on smaller components.
This technique is particularly valued in industries like electronics, where it's used to produce precision components such as circuit boards, semiconductors, and microelectromechanical systems (MEMS). To explore more about the various applications of chemical etching, you can visit this page. The benefits of chemical etching include high precision, the ability to create complex geometries without inducing mechanical stress, and the capability to work with a wide variety of materials, including metals, glass, and ceramics.
Key Differences Between Chemical Milling and Etching
While chemical milling and etching share similarities, they differ in several key aspects:
- Material Compatibility: Chemical milling is generally used for larger parts made from materials like aluminum and titanium, where substantial material removal is needed. Chemical etching, on the other hand, is suitable for a wider range of materials, including metals, glass, and ceramics, and is ideal for smaller, more intricate components.
- Precision and Tolerances: Chemical etching excels in precision, making it ideal for applications requiring fine details and tight tolerances. Chemical milling is less precise, focusing on reducing material thickness or creating larger features on parts.
- Cost Implications: Chemical milling typically involves higher initial costs due to the need for custom masking and handling of large parts. In contrast, chemical etching is generally more cost-effective for producing high volumes of small, intricate parts, especially when design flexibility is required.
FAQs for Scaling Up Production with Chemical Milling and Etching
What are the key considerations when transitioning from prototype to large-scale production using chemical milling and etching?
When moving from prototype to large-scale production, it’s crucial to assess production volume, material compatibility, and the required level of automation. Ensure that the process is optimized for efficiency and that the design is compatible with chemical milling or etching techniques. A feasibility study can help identify potential issues before scaling up.
What strategies can help in reducing costs while scaling up production with chemical milling and etching?
Cost reduction strategies include water conservation, optimizing cooling systems, automating chemical control, and carefully managing material usage. Recycling resources, such as water, and monitoring energy consumption can also significantly reduce operational costs without compromising quality.
How can I ensure high yields and quality in my scaled-up production process?
To maximize yields and quality, focus on automating critical processes, rigorously testing raw materials, and closely monitoring the chemical parameters of the etching process. Ensuring that the machinery is fine-tuned and that materials are sourced from reliable suppliers will also contribute to consistent, high-quality output.
Wrapping Up: Chemical Milling & Etching are Viable Options for Scaling Production
Scaling up production with chemical milling and etching is a viable option for engineers looking to maintain precision and quality while increasing throughput. By understanding the nuances of each process, optimizing key production factors, and implementing cost-saving strategies, you can successfully transition from prototype to large-scale manufacturing.
Chemical milling and etching offer unique benefits that, when applied correctly, can significantly enhance productivity and yield, making them essential tools in modern manufacturing.
When it comes to scaling up with confidence, working with Chemcut provides you with the expertise and customized solutions needed to optimize your process from start to finish. Contact us today to learn how we can help you achieve efficient, high-quality production tailored to your specific needs.